Quand l’industrie devient digitale : les perspectives de la continuité numérique
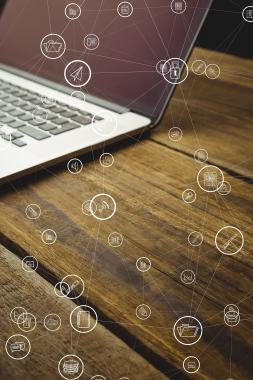
À l’ère de l’industrie 4.0, la continuité numérique offre de nouvelles perspectives aux industriels. Toutefois, elle implique une nouvelle organisation en interne, afin d’en exploiter toutes les opportunités. Retour sur les différents enjeux de la continuité numérique, avec Laurent Carlion, directeur marketing et technique France chez ifm electronic.
Considérée comme une « révolution industrielle », la transition numérique de la production industrielle a déjà fait entrer l’industrie dans une nouvelle ère. Et celle-ci n’est pas réservée aux nouvelles usines. Tant ses perspectives et avantages sont nombreux, elle s’impose auprès de l’ensemble de l’écosystème, du grand groupe à la PMI.
Si la digitalisation de la production industrielle est amorcée, assurer la continuité numérique est assurément la prochaine étape. Elle permet de relier un ensemble de données, relatives au produit ou au service tout au long de son cycle de vie : conception, production, utilisation en conditions réelles, service après-vente, recyclage… Ces données deviennent accessibles à chaque instant, pour tous les acteurs impliqués, via des standards dorénavant unifiés (IO Link, OPC UA , MQTT, etc.).
La continuité numérique, une approche attractive pour l’industrie
La digitalisation apporte son lot de changements dans le secteur industriel, et la continuité numérique tend à y apporter toujours plus de bénéfices. À la clé, une prise de décision plus rapide, par exemple. Les tâches sans valeur ajoutée peuvent être automatisées plus facilement, les frontières entre OT et IT tendent à disparaître. La continuité numérique permet également d’améliorer la disponibilité des machines, grâce aux progrès de la maintenance prédictive. Il est ainsi possible de prévoir une éventuelle panne de pièce, de contrôler si la pièce correspondante est en stock, de consulter les personnes en capacité d’intervenir, le tout rapidement, grâce à l’accessibilité des données. Et de réaliser la maintenance à distance – ce qui devrait amener à la création de nouveaux produits et services. Laurent Carlion y décèle également un autre avantage : l’attractivité des métiers de l’industrie. « En digitalisant la production industrielle, nous utilisons des outils à forte valeur ajoutée, qui rendent certainement plus séduisants les métiers de l’industrie. Nous sommes loin du cliché de la ‘caisse à outils’ qui perdure dans l’imaginaire commun ! » Indéniablement, la continuité numérique est un gage de productivité. De quoi améliorer la compétitivité des entreprises qui se l’approprient.
C’est dans ce contexte qu’a été créé le collectif continuité numérique (CCN), par huit entreprises : ifm electronic, Inetum, SICK, SEW, Staubli, Phoenix contact, Festo et SAP. Leur objectif : partager expérience et bonnes pratiques dans les rapprochements des services de l’OT et de l’IT, qui n’ont pas systématiquement le même langage et les mêmes approches au départ. Chaque entreprise du collectif apporte ainsi son expertise, dans un domaine différent. Du capteur à l’ERP, ensemble, elles disposent de toutes les briques technologiques et peuvent mener des projets en commun. « Le rapprochement de nos supports techniques était déjà une vraie aventure humaine ! Travailler ensemble a changé notre manière d’aborder le marché, ensemble, avec une solution globale, précise Laurent Carlion. Quelque part, nous changeons aussi notre business model. » Le CNN a notamment réalisé une nouvelle génération de machines, à partir de machines d’assemblage 3.0 de la société ATS : le concept machine 4.0, Axelle. Capteurs intelligents, éléments de vision, éléments pour améliorer la maintenance prédictive et le suivi énergétique… Le CCN a ensuite partagé les avantages de ces ajouts technologiques pour différents métiers de l’industrie (opérateur, responsable de maintenance, directeur d’usine…), ainsi que pour le client final.
Repenser l’organisation des entreprises
Pour profiter de l’ensemble des opportunités offertes par la continuité numérique, l’enjeu est avant tout de réussir à se réorganiser en interne, souligne Laurent Carlion : « Le défi est plus organisationnel que technologique : nous disposons de tous les outils nécessaires à la mise en place de la continuité numérique. Le tout est de mener une conduite de changement en interne en impliquant l’ensemble des services afin d’en profiter pleinement ». Parmi les changements en profondeur, l’apparition de nouveaux métiers fait également son chemin dans le secteur industriel, à l’image du Data Analyst par exemple, qui exploite les données recueillies.
Par ailleurs, le besoin de formation, à tous les échelons de l’entreprise, se fait également sentir afin de s’assurer que chacun maîtrise ces nouvelles technologies. « Les collaborateurs doivent également être en capacité de s’adapter et de faire preuve d’agilité par rapport à ces nouveaux systèmes mis en place. Il s’agit d’un véritable changement des méthodes de travail, avec des accès plus larges aux informations, à tous les niveaux de l’entreprise », ajoute Laurent Carlion.
Continuité numérique et industrie 4.0 : s’emparer des nouveaux défis
D’autres défis attendent l’industrie 4.0 pour les années à venir, à commencer par l’enjeu climatique, qui vient de pair avec la hausse du coût de l’énergie. « Le développement d’une industrie plus verte est fondamental pour les années à venir : nous devons réfléchir à une production plus responsable, moins gourmande en énergie et en moyens, souligne Laurent Carlion. La continuité numérique nous permettra par exemple de remonter les données de consommation ». Pour une industrie plus vertueuse !
Une chose est sûre, l’industrie 4.0 sera un pilier du développement de l’industrie française et de la réindustrialisation. « En attirant de nouveaux talents et en étant plus compétitif, nous allons pouvoir produire plus facilement en France, à des coûts plus attractifs et en privilégiant les circuits courts », conclut Laurent Carlion.
Nos autres actualités
Tout voirRejoignez la plus grande communauté de fournisseurs industriels
- Vous aider dans votre veille technologique permanente
- Vous offrir des statistiques fournisseurs détaillées
- Vous offrir une visibilité à l’internationnal
Découvrez le plus grand catalogue de produits industriels du marché
- Vous offrir le meilleur catalogue de produits industriels du marché
- Vous garantir une plateforme 100% sécurisée
- Vous permettre des échanges à distance en direct