When the industry goes digital: the prospects for digital continuity
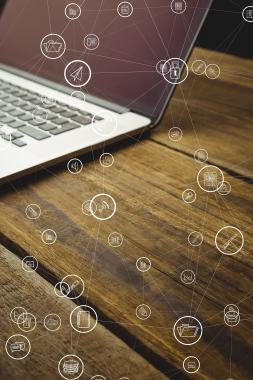
In the era of Industry 4.0, digital continuity offers new perspectives to manufacturers. However, it involves a new internal organization, in order to exploit all the opportunities. A look back at the various challenges of digital continuity, with Laurent Carlion, marketing and technical director France at ifm electronic.
Considered an “industrial revolution”, the digital transition of industrial production has already ushered the industry into a new era. And this isn't just for new factories. As its prospects and advantages are numerous, it imposes itself on the entire ecosystem, from the large group to the PMI.
If the digitization of industrial production has begun, ensuring digital continuity is certainly the next step. It makes it possible to link a set of data relating to the product or service throughout its life cycle: design, production, use in real conditions, after-sales service, recycling, etc. This data becomes accessible at all times, for everyone. the players involved, via now unified standards (IO Link, OPC UA, MQTT, etc.).
Digital continuity, an attractive approach for the industry
Digitization brings its share of changes in the industrial sector, and digital continuity tends to bring ever more benefits. The key is faster decision-making, for example. Tasks without added value can be automated more easily, the boundaries between OT and IT tend to disappear. Digital continuity also improves machine availability, thanks to advances in predictive maintenance. It is thus possible to predict a possible breakdown of a part, to check whether the corresponding part is in stock, to consult the people able to intervene, all quickly, thanks to the accessibility of the data. And to carry out remote maintenance – which should lead to the creation of new products and services. Laurent Carlion also sees another advantage: the attractiveness of industrial professions. “By digitizing industrial production, we are using tools with high added value, which certainly make industrial jobs more attractive. We are far from the cliché of the 'tool box' which persists in the common imagination! Undeniably, digital continuity is a guarantee of productivity. What improve the competitiveness of companies that appropriate it.
It is in this context that the digital continuity collective (CCN) was created by eight companies: ifm electronic, Inetum, SICK, SEW, Staubli, Phoenix contact, Festo and SAP. Their objective: to share experience and best practices in bringing together OT and IT services, which do not always have the same language and the same approaches at the outset. Each company in the collective thus contributes its expertise in a different field. From sensor to ERP, together they have all the technological building blocks and can carry out joint projects. “Bringing together our technical support was already a real human adventure! Working together has changed our way of approaching the market, together, with a global solution, explains Laurent Carlion. Somehow, we are also changing our business model. In particular, the CNN has produced a new generation of machines, based on ATS 3.0 assembly machines: the 4.0 machine concept, Axelle. Smart sensors, vision elements, elements to improve predictive maintenance and energy monitoring… The CCN then shared the advantages of these technological additions for different trades in the industry (operator, maintenance manager, plant manager…), as well as for the end customer.
Rethinking business organization
To take advantage of all the opportunities offered by digital continuity, the challenge is above all to succeed in reorganizing internally, emphasizes Laurent Carlion: "The challenge is more organizational than technological: we have all the tools necessary for establishment of digital continuity. The key is to conduct change internally by involving all departments in order to take full advantage of it”. Among the in-depth changes, the emergence of new professions is also making its way into the industrial sector, like the Data Analyst for example, who uses the data collected.
In addition, the need for training, at all levels of the company, is also felt in order to ensure that everyone masters these new technologies. “Employees must also be able to adapt and show agility in relation to these new systems put in place. This is a real change in working methods, with broader access to information, at all levels of the company,” adds Laurent Carlion.
Digital continuity and industry 4.0: seizing new challenges
Other challenges await Industry 4.0 for the years to come, starting with the climate issue, which comes hand in hand with the rising cost of energy. “The development of a greener industry is fundamental for the years to come: we must think about a more responsible production, less greedy in energy and resources, underlines Laurent Carlion. Digital continuity will allow us, for example, to trace consumption data.” For a more virtuous industry!
One thing is certain, industry 4.0 will be a pillar of the development of French industry and reindustrialisation. “By attracting new talent and being more competitive, we will be able to produce more easily in France, at more attractive costs and favoring short circuits,” concludes Laurent Carlion.
Our other news
See allJoin the largest community of industrial suppliers
- Helping you with your ongoing technology watch
- Provide you with detailed supplier statistics
- Give you international visibility
Discover the largest catalogue of industrial products on the market
- To offer you the best catalogue of industrial products on the market
- To guarantee you a 100% secure platform
- Enable you to have live remote exchanges