Implementation and benefits of predictive maintenance of hydraulic industrial facilities
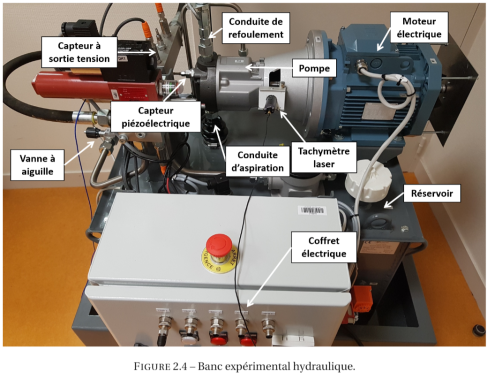
In the industrial sector and on hydraulic industrial installations in particular, the occurrence of a breakdown can have heavy financial consequences. Fortunately, it is possible to limit and anticipate these incidents thanks to predictive maintenance. Hugo André, Lecturer at the University of Saint-Etienne , explains the advantages of predictive maintenance and the monitoring actions to be implemented.
Predictive maintenance: anticipate to better protect
Predictive maintenance, also called predictive, consists of finely and repeatedly monitoring the performance of an installation or its main components in order to limit operating faults – or better manage their resolution thanks to maintenance operations triggered in the event of a fault. real need. "It's not about making predictions, which is why I prefer the term predictive maintenance" , specifies Hugo André. On industrial installations, we know that faults can occur and we also know how to prevent them. Predictive maintenance assesses the health of the monitored system in order to program an action that will prevent an unexpected failure . The more costly the impact of a failure is from an operational point of view, the more comprehensive, technical and proactive the maintenance strategy employed will be ”.
Predictive maintenance is centered on the state of the installation but also on its reliability. In the case of hydraulic industrial installations (steel works, lifting and handling, exploitation of shale gas, geothermal installations, etc.), the systems are complex. " Certain elements, particularly sensitive, are to be monitored ", explains the head of the Industrial Engineering and Maintenance department of the University of Saint-Etienne:
- Proportional distributors: these elements are useful for slaving a system to a given speed or position. “ They are the result of very fine machining and the slightest particle present in the fluid can block the system . »
- Valve seats: useful for holding the system in position. “ Wear caused by the friction of particles causes sealing problems ”.
- Hydraulic pumps and motors: “ they load the system and are sensitive to particles or other cavitation problems ”, ie the formation of gas bubbles.
In 70% of hydraulic system failures, fluid pollution is the cause. It is therefore necessary to put in place measures adapted to the systems in order to limit incidents as much as possible.
Predictive maintenance of hydraulic installations: the points of vigilance
Two main applications attributed to hydraulic systems can be distinguished. The first is the hydraulic control system, in a closed system, which makes it possible to increase the force tenfold and which is found in many industries (construction, handling, steelworks, etc.). In this system, the liquid (oil or water) is introduced and then operates autonomously, without the need for a continuous supply. " This greatly facilitates monitoring", underlines Hugo André. In these closed systems, the composition of the fluid is checked preventively. Three points are to be studied:
- The presence of metal in the liquid;
- The presence of water in the oil, which can be caused by a faulty seal and can cause corrosion or cavitation (formation of gas and vapor bubbles);
- The presence of gas, due to a cavitation problem.
Hydraulic pumping systems, in an open system, aim to pressurize a fluid to create a flow in a given direction. “ This applies in particular in heavy industry which uses a lot of water for cleaning or cooling, for example ”. In this type of installation, the circulating liquid is constantly renewed. “ The analysis of this liquid is decorrelated from the state of health of the hydraulic system. It will therefore be necessary to find other monitoring methods that are based on the analysis of other physical properties such as instantaneous pressure and instantaneous speed ", sums up the Head of the signal processing axis for the LASPI industry . from the University of Saint-Etienne.
Predictive maintenance: targeted actions according to the installations
The maintenance of hydraulic installations in a closed system is mainly based on the analysis of lubricating fluids. “ This analysis is most often manual and is then based on periodic oil samples analyzed in the laboratory. It is a human intervention and therefore discontinuous ”, explains Hugo André. For constant monitoring and rapid analysis of the results, remotely, the use of a connected oil condition monitoring system is recommended. Its interest is to provide directly, online, precise information on the condition of lubricants but also on the proper functioning of hydraulic systems. This monitoring makes it possible to plan an appropriate maintenance schedule but also to limit the risk of failures.
To perform predictive maintenance of open systems, pressure trend sensors and piezoelectric vibration sensors are used. The latter, electronically wired to a recorder, works like a stethoscope. “ We know how to analyze the vibration produced by the machine to detect faulty behavior through its frequency content. Recently, we showed at LASPI that the study of the instantaneous pressure or the instantaneous speed of rotation also makes it possible to detect such anomalies. We modeled the behavior of a pump and validated experimentally that pump faults (axial pistons used in construction, for example) could be diagnosed by all these means. This work was carried out for the benefit of an industrial company currently in the development phase of new pumps”.
This anticipation is an important point: the earlier predictive maintenance is considered in the development of the installation, the more it will be adapted and therefore effective. We can thus think about the instrumentation of the pump from the design stage but also limit the problems: lack of space for the sensor, accessibility of the pump (some pumps are buried), erroneous evaluation of the initial state of the machine.
The concrete benefits of predictive maintenance
For hydraulic industrial installations, predictive maintenance strategies are strongly recommended for the safety of the teams and for the financial optimization of the equipment. “It is a mistake to imagine that we will only win on the price of the element that we protect and which is ultimately low in terms of production losses. Predictive maintenance actually makes it possible to optimize production time: the more you are surprised by a breakdown, the longer the downtime is likely to be with more equipment impacted, longer and incompressible delivery times, etc. summarizes Hugo André.
Predictive maintenance therefore limits breakdowns and the financial losses associated with them. It increases the lifespan of equipment and their operating time by making it possible to plan the maintenance interventions that are really necessary. An investment that also contributes to reducing curative maintenance costs.
Our other news
See allJoin the largest community of industrial suppliers
- Helping you with your ongoing technology watch
- Provide you with detailed supplier statistics
- Give you international visibility
Discover the largest catalogue of industrial products on the market
- To offer you the best catalogue of industrial products on the market
- To guarantee you a 100% secure platform
- Enable you to have live remote exchanges