Automating your workshop is good, thinking about it beforehand is better!
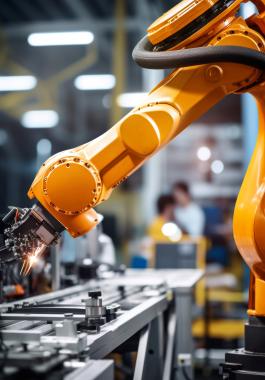
It’s a Prévert-style list, as the reasons for negotiating the shift to automation of machining operations are becoming crucial. Business managers, machinists, workshop managers, engineers, all are aware that reducing operating costs requires automation. The range of solutions offered and the promising equipment on the market today are numerous. Before getting started, you should ask yourself some useful questions…
During the last Global Industrie Lyon 2023 show, 49% of visitors and exhibitors surveyed declared that topics around automation were part of the priority roadmaps. This result, taken from the “2nd Industry Innovation Barometer” carried out by the SATT Network and Global Industrie, demonstrates how automation has become one of the topics of the moment.
“Machining workshops are gradually moving towards total automation” estimates Thomas Janquart, founder of Armin Robotics, in the journal Industrie et Technologies. As an integrator, the Belgian company - specializing in robotic solutions for machining - offers fully integrated robotic cells whose control is managed by a single software. This vision of the market is supported by the latest World Robotics report, published by the International Federation of Robotics. Last September, the Federation wrote on this subject that “it is rather general industry which will continue the modernization and decarbonization of its production capacity”.
The shift towards workshop modernization is easily explained. Let us recognize that in recent years, the manufacturing industry has been put to the test. Between geopolitical changes, a global pandemic with multiple consequences, and a shortage of workers with the manual, operational and technical skills required for traditional NC machining processes, they must find ways to increase production without increasing their labor requirements. -work. In fact, reducing reliance on human intervention in favor of the repeatability and predictability associated with automation reduces production cycle times and improves quality and planning capacity.
Thinking about your new workshop…
First commandment! “80% of human tasks are repeatable, therefore automatable. However, there remains a 20% that requires human judgment. This part is extremely difficult to automate and would be very expensive. Humans are therefore not ready to be replaced in your factories. The key to successfully implementing automation is not to try to replace it, but to merge the expertise and judgment of your employees with robotics to maximize the performance of the task to be performed,” advise the experts at APR.
And, even though automation encompasses many concepts, from feeding raw material bars onto a lathe, to reducing operator intervention, to increasing operating times with less personnel or by fully automated intelligent manufacturing systems, the user must bear in mind that the overall performance of the workshop is greatly increased – more productivity, flexibility and quality – thanks to different sources of optimization .
We must, in fact, focus on the detection and reduction of time lost in the journey of the part, but also on the significant increase in production capacity thanks to a machine environment designed for autonomous and secure operation 24 hours a day – 7 days a week, while keeping in mind the reduction in adjustment times for a first part.
It is also necessary to think about the reliability and optimization of processes continuously by collecting internal information to improve in real time the productivity factors (cycle time, tool longevity, etc.) and quality of a part on the basis of the experience of the preceding machining operations. The flexibility and interchangeability of means allowing production to be smoothed (elimination of bottlenecks and improvement of part flows) must be taken into account, as is the reduction in product launch times: from the customer's ERP to to the final development by the operator of a pre-series or a prototype. Finally, integrating functionalities specific to the specificity of manufacturing, the production organization and the external environment is also required.
Go even further…
The 4.0 environment is not limited to a digital dimension to act on production. Example. In its new catalog, Erowa offers “latest generation solutions to lay the foundations for the workshop of the future. Clamping and part positioning systems, robots, measuring and pre-adjusting machines help to raise the level of performance compared to common equipment. They are suitable for any size of part and any type of process: milling, turning, grinding, marking, etc. »
In the field of robotics, “developments focus on new priorities: anticipated movement management, increasing the capacity of part flows, securing movements, zones, communicating pallets, use of autonomous connected systems, etc. For example, even with limited equipment, the ERD 150L robot offers an interesting concept. It is completely scalable and can extend its scope to an ever-increasing number of devices. Acquiring a robot for each machine installation is no longer the best solution for efficiently managing a workshop. Ergonomics remains the common thread for all components of the installation in a workshop,” we advise at Erowa.
Successfully implementing automation in a factory requires time, reflection and active monitoring, including a visit to the Global Industrie show, where all the solutions are within reach!
Our other news
See allJoin the largest community of industrial suppliers
- Helping you with your ongoing technology watch
- Provide you with detailed supplier statistics
- Give you international visibility
Discover the largest catalogue of industrial products on the market
- To offer you the best catalogue of industrial products on the market
- To guarantee you a 100% secure platform
- Enable you to have live remote exchanges