The Future of Industrial Lubrication: How SDT’s Ultrasound Technology is Revolutionizing Maintenance Practices
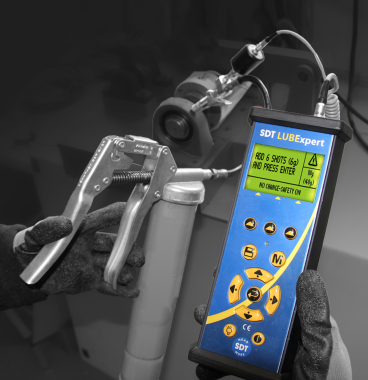
Introduction
In the world of industrial manufacturing, the importance of lubrication cannot be overstated. From radial and axial bearings to complex gearboxes, lubrication plays a pivotal role in ensuring machinery runs smoothly and efficiently. However, traditional methods of lubrication maintenance have their limitations, often leading to costly downtime and safety risks. This article delves into the challenges of lubrication in industrial settings and introduces SDT International’s groundbreaking ultrasound technology as the ultimate solution for these issues.
The Lubrication Conundrum in Industrial Manufacturing
Lubrication is the lifeblood of industrial machinery, offering a plethora of benefits such as reducing wear, absorbing shock, and dissipating heat. Yet, despite its critical role, lubrication maintenance is fraught with challenges. According to industry studies, 34.4% of bearing failures are attributed to inadequate lubrication. Manual lubrication systems, although common, are time-consuming and fraught with human error. Even automatic systems like splash and pressure lubrication have their drawbacks in terms of precision and cost.
The Cost of Inadequate Lubrication
The repercussions of poor lubrication are not just mechanical but also financial and environmental. A single bearing failure in a paper mill, for instance, can result in enormous maintenance and component replacement costs, not to mention the lost revenue from unscheduled downtime. Inconsistent lubrication can also lead to increased energy consumption, contributing to a larger carbon footprint.
“According to a major ball bearing company, 54% of bearing failures are lubrication related. In a study by the Massachusetts Institute of Technology (MIT), it was estimated approximately $240 billion is lost annually across U.S. industries due to downtime and repairs for manufacturing equipment damaged by poor lubrication. Improper bearing lubrication or re-lubrication accounts for up to 50% of machine failures.” (source: https://insights.globalspec.com/article/13580/the-true-cost-of-bearing-lubrication)
SDT International: The Future of Lubrication Maintenance
Enter SDT International, a global leader in ultrasound technology, specializing in condition monitoring of assets and energy savings. SDT’s mission is to provide ultrasound solutions that help customers gain a better understanding of the health of their factory. Their technology is designed to predict failures, control energy costs, and improve product quality, thereby contributing to the overall reliability of assets.
Bearing Lubrication Monitoring: A Case Study
One of the eight applications developed by SDT is Bearing Lubrication Monitoring. This application leverages advanced ultrasound technology to provide real-time data on the condition of lubricants within bearings. It can detect issues like over-lubrication or under-lubrication long before they become critical, allowing for timely intervention. This not only extends the lifespan of the machinery but also significantly reduces maintenance costs and downtime.
Why Choose SDT?
- Precision: SDT’s ultrasound technology offers unparalleled accuracy in monitoring lubricant conditions.
- Cost-Efficiency: By predicting failures and reducing downtime, SDT helps industries save tens of thousands of dollars.
- Environmental Benefits: Efficient lubrication monitoring leads to lower energy consumption, aligning with sustainability goals.
- Safety: Real-time monitoring minimizes risks, ensuring a safer working environment.
Conclusion
The challenges of lubrication maintenance in industrial manufacturing are many, but they are not insurmountable. With SDT International’s ultrasound technology, industries can now look forward to a future where machinery runs smoother, costs are contained, and the environment is respected. It’s not just an evolution; it’s a revolution in how we approach lubrication and machinery maintenance.
Our other news
See allJoin the largest community of industrial suppliers
- Helping you with your ongoing technology watch
- Provide you with detailed supplier statistics
- Give you international visibility
Discover the largest catalogue of industrial products on the market
- To offer you the best catalogue of industrial products on the market
- To guarantee you a 100% secure platform
- Enable you to have live remote exchanges